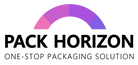

NEWS
All PACK HORIZON NEWS
EN ES FR DE IT
Time: 2024-02-05
23 Surface Treatment Processes
The surface treatment process for cosmetic packaging materials is the result of effectively integrating colors, coatings, techniques, and equipment. Different processes create varied effects on the finished packaging products. In this article, we will take a quick look at 23 surface treatment techniques.
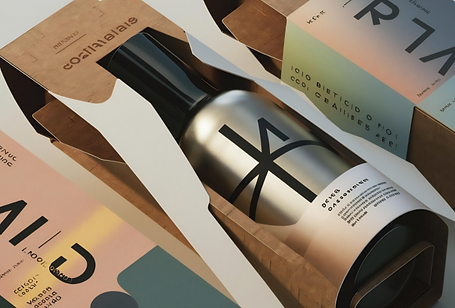
Table of contents
1~5 Spray Painting/Electroplating/Vacuum Plating/IMD/Screen Printing
6~10 Pad Printing/Hydrographic Printing/Heat Transfer Printing/Dye Sublimation/Baking Paint
11~15 Anodizing/Mechanical Brushing/Laser Engraving/High-Gloss Edge Cutting/Guilloché Engraving
16~20 Sandblasting/Etching/Polishing/Hot Stamping/Flocking
21~23 Out-of-Mold Decoration/Self-Healing Coating/Nano Waterproof Coating
1 / Spray Painting
-
Spray Painting: The most common surface treatment, applicable to both plastic and metal. Includes spray coating (liquid paint) and powder coating. Paint typically consists of resin, pigment, solvent, and additives. Plastic spray painting usually involves two layers: a colored topcoat and a transparent protective top layer.
-
Process:
-
Pre-cleaning (e.g., electrostatic dust removal).
-
Topcoat spraying (visible color layer).
-
Drying (natural or oven drying).
-
Cooling (required for oven drying).
-
Protective clear coat spraying.
-
Curing the protective layer.
-
QC inspection.
-
-
Rubber Paint (Elastic Paint): A two-component, high-elasticity tactile paint that creates a soft, rubber-like finish. Widely used for electronics, mobile phone cases, and beauty tools. Drawbacks include high cost and durability issues.
-
UV Paint: Cures under UV light (200–450 nm wavelength). Features high transparency, hardness, fast curing, and enhanced surface protection.
2 / Electroplating (Water Plating)
-
An electrochemical process where metal is deposited onto a substrate immersed in an electrolyte solution.
-
Materials: Primarily ABS (electroplating-grade). Common finishes: gold, silver, black, gunmetal.
-
Effects: High-gloss, matte, frosted, or mixed finishes.
3 / Vacuum Plating
-
A vacuum-based method to deposit thin metal layers.
-
Process: Cleaning → primer spraying → baking → vacuum plating → topcoat spraying → QC.
-
Pros:
-
Compatible with more plastics.
-
Colorful finishes, eco-friendly, non-conductive options.
-
Brighter than electroplating.
-
-
Cons: Higher defect rates, higher cost, and lower wear resistance (requires UV protection).
4 / IMD (In-Mold Decoration)
-
Overview: Combines printing, molding, and injection molding for durable, scratch-resistant finishes. Ideal for complex shapes and backlit designs.
-
Types:
-
IML: 2D products (no stretching).
-
IMF: 3D products (high-pressure forming).
-
IMR: Leaves only ink on the surface (hot stamping).
-
-
Advantages: Scratch resistance, 3D effects, customizable colors, precise patterning.
5 / Screen Printing
A traditional method using a mesh stencil to transfer ink. Suitable for flat or slightly curved surfaces (paper, plastic, glass, etc.).
6 / Pad Printing
Prints on irregular surfaces (e.g., phone keypads, instruments). Uses a silicone pad to transfer ink from an etched plate.
7 / Hydrographic Printing (Water Transfer)
-
Transfers patterns via water-soluble film.
-
vs. IMD: Less precise positioning, limited edge coverage, and potential fading.
8 / Heat Transfer Printing
Uses pre-printed films to transfer high-resolution designs onto surfaces (ABS, wood, coated metal). Common in cosmetics, toys, and packaging.
9 / Dye Sublimation
Embeds dye into materials (20–30 µm depth) for fade-resistant, vibrant colors. Used in electronics (e.g., Sony VAIO laptops).
10 / Baking Paint
Heat-cured paint for enhanced durability and gloss. Piano Lacquer: A multi-layer, high-gloss finish resistant to heat and scratches.
11 / Anodizing
-
Electrochemical oxidation for metals (e.g., aluminum).
-
Process: Cleaning → anodizing → dyeing → sealing.
-
Applications: Decorative, protective, or functional finishes. Secondary Anodizing: Creates multi-color or embossed logos.
12 / Mechanical Brushing
Creates linear or random patterns on metal surfaces (aluminum, stainless steel).
13 / Laser Engraving
Uses lasers to etch designs. Suitable for metals, plastics, and more. Laser Brushing: Creates textured patterns with tactile depth.
14 / High-Gloss Edge Cutting
Polishes metal edges (e.g., aluminum) via CNC machining. Common in electronics.
15 / Guilloché Engraving
Mechanical engraving for decorative textures (e.g., metal logos).
16 / Sandblasting
Blasts surfaces with abrasives for cleaning, texturing, or prep. Applications: casting cleanup, anti-slip finishes, matte effects.
17 / Etching
Chemically engraves metal for fine patterns or micro-features. Used in molds and decorative surfaces.
18 / Polishing
Creates glossy or matte finishes via mechanical, chemical, or electrolytic methods.
19 / Hot Stamping (Foiling)
Transfers metallic foil using heat/pressure. Enhances aesthetics and anti-counterfeiting (e.g., cigarette packaging).
20 / Flocking
Adheres fibers to surfaces for texture or protection (e.g., jewelry boxes, automotive interiors).
21 / Out-of-Mold Decoration
Combines molding with surface decoration (e.g., fabric-wrapped phone cases).
22 / Self-Healing Coating
Repairs minor scratches via heat-activated polymer flow. Used in automotive and future architectural applications.
23 / Nano Waterproof Coating
Thin, invisible hydrophobic layer applied via vacuum sputtering. Protects electronics, textiles, and lab equipment.
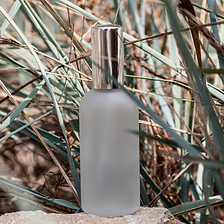
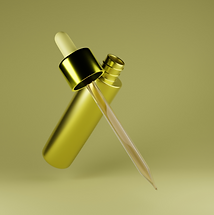

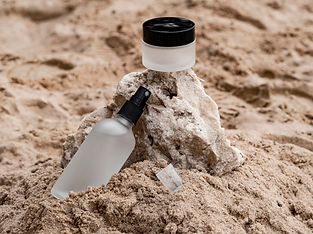

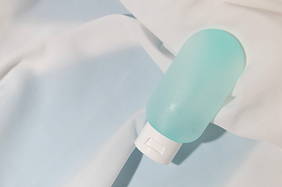



